Rovner® Products Produces Face Shields in Wake of COVID-19
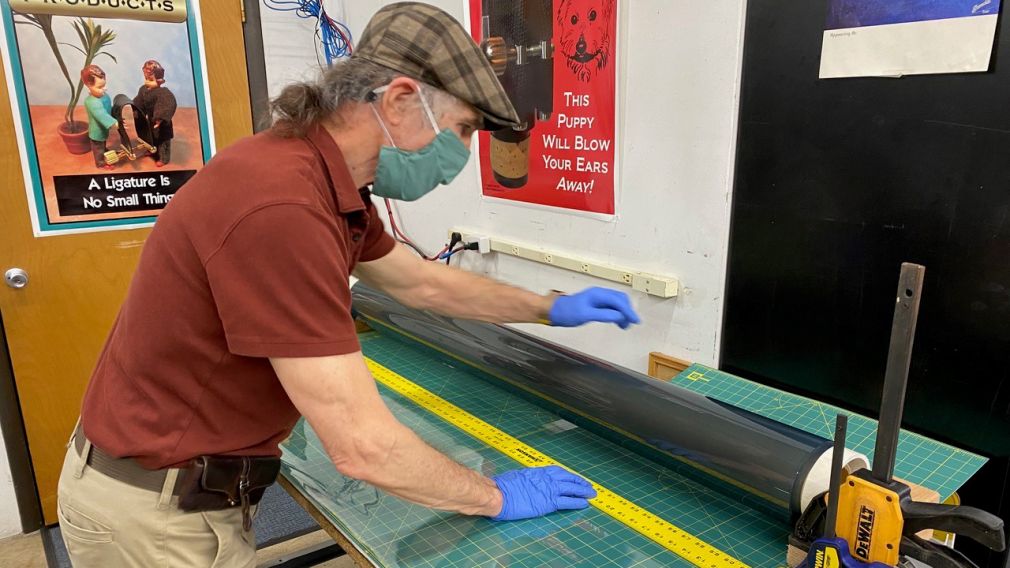
Rovner® Products started temporarily manufacturing face shields at the end of March when the Governor of Maryland closed non-essential business and regular production was shut down. After seeing the pleas for personal protective equipment (PPE) from healthcare professionals, George and Lynn Reeder felt compelled to step up and re-purpose their idle manufacturing equipment. The NAMM Member has made a significant impact since the project launched just a few months ago.
Rovner Products began with the construction of the original Dark Ligature, a device which holds a reed onto the mouthpiece of a single-reed instrument, in 1974. Company founder, Phil Rovner’s background in mechanical engineering, acoustic technology, and music theory was the basis for creating ligatures that “set a new convention for ligature design and performance.”
The Reeders purchased Rovner Products from Rovner in 2014 and brought the company up to date when the facility was reconfigured for better flow, scrutinized and fine-tuned every process, and brought forth plans to purchase state of the art manufacturing equipment. We recently sat down with Lynn Reeder to discuss the shift in operations to support the fight against the COVID-19 pandemic.
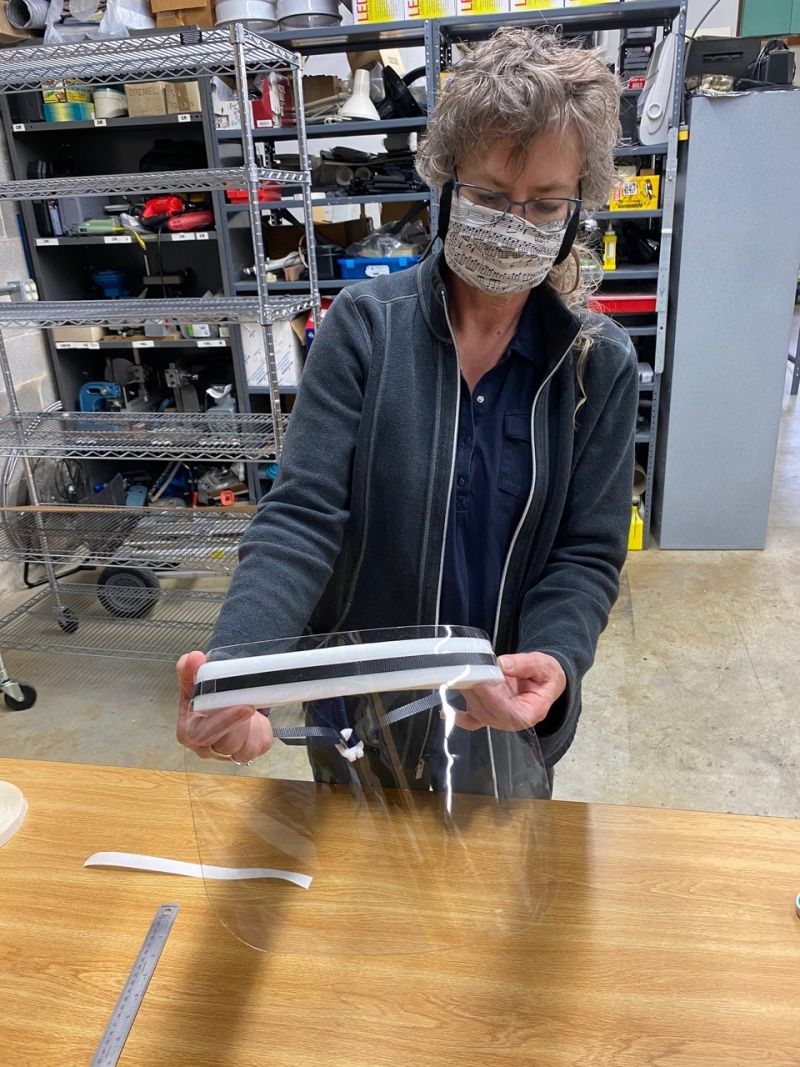
Could you provide a brief description of the research and development process for your face shields?
The R&D process was both hilarious and frustrating. By the time we got started, it seemed like everybody in the world was working on creating masks and shields to either sell or donate. We started by scanning the internet and most ‘homemade’ versions involved a thin plastic sheet with foam stuck to the top and elastic stapled on. We then scavenged our basement and garage for anything we could find to start working on our prototype. Luckily, I used to be a professional craft designer and George is extraordinarily handy, so we have lots of ‘stuff’ around the house.
For our first run, we cut plastic from a giant vinyl zipper bag that holds a comforter, paired it with pipe insulation for foam and secured with staples. It was all awful. Finding any kind of viable raw goods was so challenging at the time that we almost gave up. We found success in procuring vinyl when a friend who is involved in boating found a source for vinyl. It was important to come up with a design that not only looked good while adding an extra measure of protection but also offered good visibility and was durable enough to reuse.
How difficult was it to alter the manufacturing process to start producing shields?
It wasn’t difficult in the least. We had our machinist create the drawings and had dies made to cut the parts we needed for production. The headbands were cut with a rotary blade and cutting mat. Since our state mandate allowed for some businesses to conduct minimal essential activities, and we couldn’t think of anything more essential than the need to protect frontline workers, we had two of our employees come in to help prep the parts. Overall, it was a fairly low-tech operation compared to what we’re used to, but it allowed us to participate in the grassroots effort to help out.
How many shields have been manufactured to date?
Approximately 3,000. Once we had determined the cost of the materials we needed, had a solid design and a reasonable estimate of the time it would take to make parts, we set 3,000 pieces as our goal. From the very start, we intended to donate the shields to our community, not to “pivot” like some other companies who decided to become large-scale PPE producers. This project was smaller in scale, but it came straight from the heart. We do other donations throughout the year, through our ‘Be Good, Do Good, Feel Good’ project or to organizations that solicit our help, so this was just another way for us to give back.
Could you please provide some examples of groups that have received your shields?
The first thought was to donate to the Greater Baltimore Medical Center, which is an excellent community hospital that holds a special place in our hearts because of the incredible care they have provided to George over the past several years. Thankfully, the COVID-19 cases there were at a manageable level and they were prepared to supply the hospital staff with PPE. We learned that other types of organizations were also sorely in need of equipment, including one of our neighbors at Rovner Products, a physical therapy practice we’ve used. George wandered over with a few shields to see if they’d be interested in getting any and they were so grateful, explaining that small businesses like theirs were just totally overwhelmed both procuring PPE for their employees and the added strain on their operating budgets once they could reopen.
So far, we’ve donated shields to the Health Facility Association of Maryland because they work directly with nursing homes and to Sheppard Pratt Hospital specifically for their veterans’ program as we’d heard that veterans were another heavily impacted group. We’ve also donated to a local volunteer fire department, several dentists, various types of private medical practices, a company providing in-home nursing support, to friends with compromised immune systems, a local sandwich shop, small markets, a hair salon, and even to one of our local customers, Chuck Levin’s Washington Music Center.
How did the volunteer force come about in the manufacturing process?
It took only a few days to create all the parts we needed for the shields, but I wasn’t fully prepared for the amount of time it would take the volunteers to assemble 3,000 pieces. Although the assembly process was easy, I still had to come up with some very clear instructions since people would be doing the assembly without supervision. I reached out to some dear friends we knew would be willing to help and they wound up doing most of the assembly. I also corresponded with a local Rovner Ambassador, Seth Kibel, who had been volunteering at the Maryland Food Bank. He was delighted to participate in a project that he and his wife could do with their two kids. Our son also reached out to several of his friends and even a local church, whose members were also already providing food to the community, were willing to get ‘crafty’ with us. Several of our employees also brought the project home and we assembled several hundred pieces in-house.
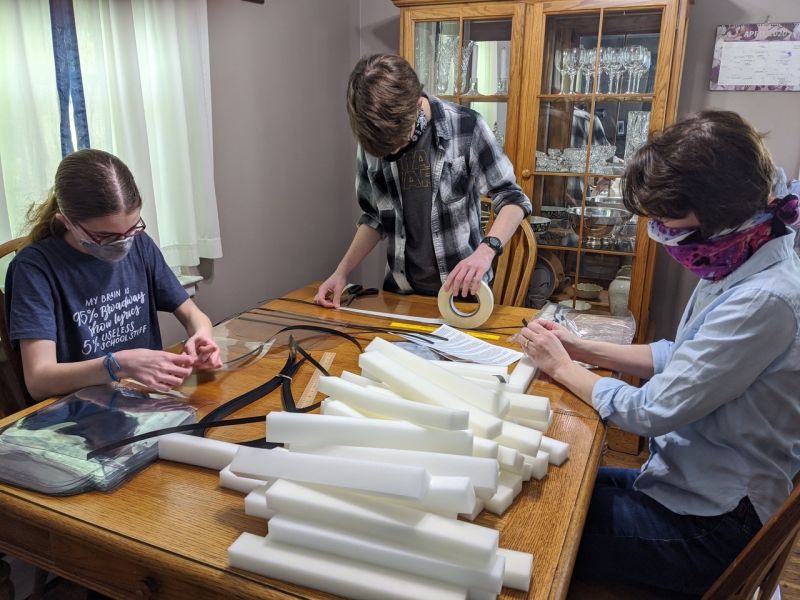
Do you have any advice for NAMM Members looking to help your initiative or to start something similar in their communities?
There are all kinds of ways to help the fight against COVID-19, so I would urge people to do anything they can, whatever moves them. Not everybody has the equipment necessary to produce shield parts, but maybe they have a sewing machine and could make masks instead. Other ideas include volunteering with a community organization like Meals on Wheels that provides other services. I urge everybody to do their part, especially by following recommended safety guidelines. This has been an overwhelming situation in every way you can think of, but both George and I feel optimistic. Above all else, keep making music! I think music is the medicine for a heartsick world, and I’m so happy to be a part of this industry.
Rovner Products “is committed to making products that truly make a difference to the woodwind player, whether eager beginner or seasoned professional.” For more information, please visit them at https://www.rovnerproducts.com/.